
Whether it's home repairs or creative DIY projects, hot glue sticks have become the tool of choice for many people with their fast curing and strong bonding. In this article, we will take an in-depth look at the core advantages of this versatile product and how to make the most of it.
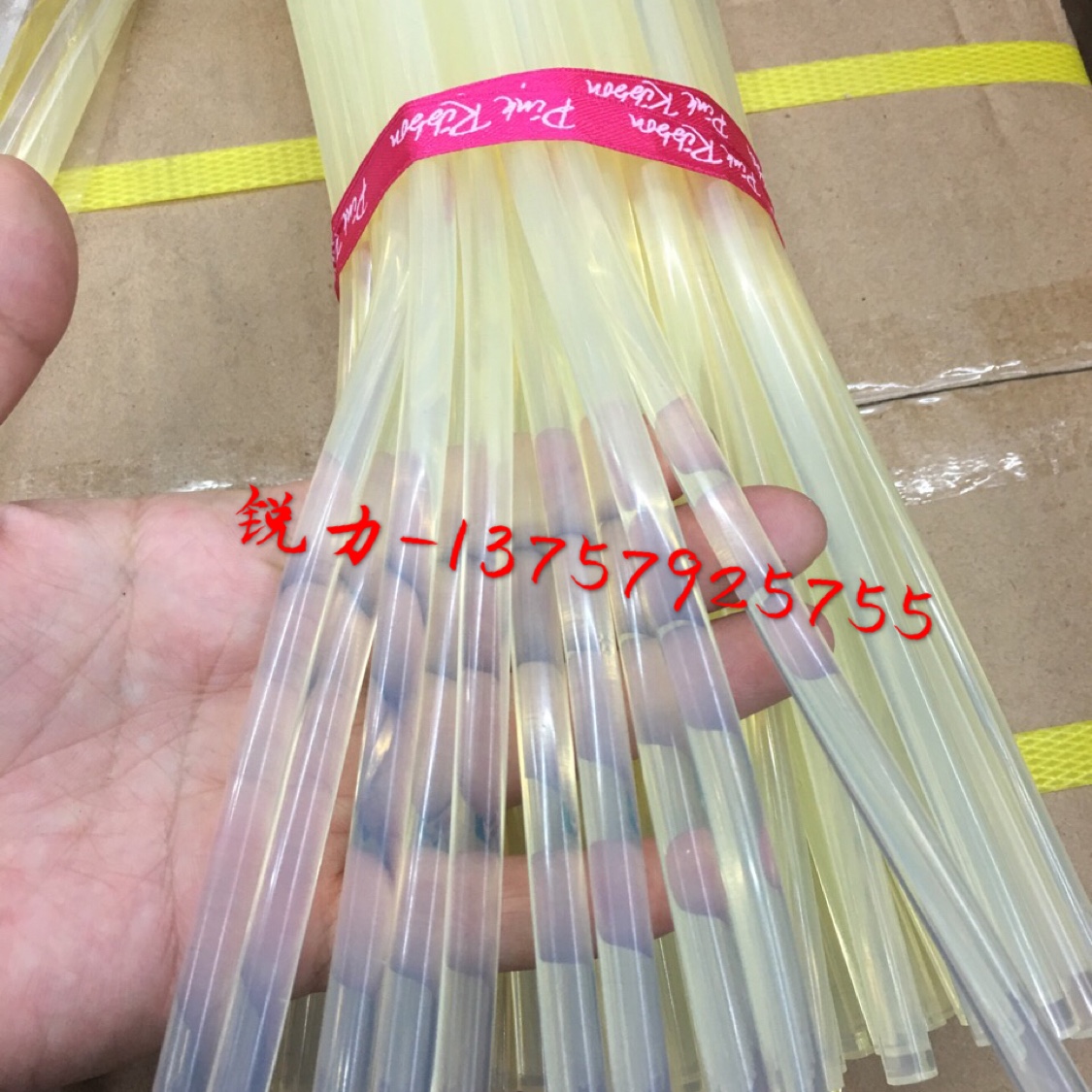
Explore the core advantages of hot glue sticks: speed and strength
The biggest feature of the hot glue stick is its efficiency and reliability. Only a few seconds of heating time, can quickly reach the ideal temperature for bonding operation. And once cooled, the adhesive force formed is very strong, suitable for the connection between various materials, including plastic, wood and even fabric.
Revealing the working principle: how to achieve instant and firm bonding
So what makes this seemingly ordinary strip object so powerful? The answer lies in the fluidity of the polyethylene resin component made of special formula after heating and melting and the strong cohesive force generated in the process of cooling and solidification. As a result, any two items can be closely combined to form a stable overall structure, which will not easily separate and fall off, and will not easily damage the joint even if pulled by external forces, thus ensuring the safety of long-term use.
From home to studio: multi-scene application examples of hot glue sticks
The application range of hot glue stick is extremely wide. It is particularly convenient and quick to repair damaged furniture or fixed decorations at home. In professional fields such as handicraft manufacturing industry, it can be used to assemble complex model components, greatly improving work efficiency. In addition, educational institutions often use it as one of the teaching aids for students to develop their hands-on skills in science experiments.
Select the hot glue stick suitable for you: full resolution of materials and specifications
There are many types of hot glue sticks available on the market, and the sizes and colors provided by different brands may vary. Generally speaking, the thinner model (about 3mm in diameter) is more suitable for fine operations such as electronic component assembly. For the assembly of large objects, it is recommend to use thicker products to increase the contact area and obtain better stability performance.
Making Full Use of Potential: Use Tips and Notes to Share
in order to ensure satisfactory results every time, please follow the following suggestions:
first, adjust the appropriate temperature range to meet the requirements of different substrate properties; Secondly, the best effect can be achieved by applying pressure evenly and continuously for a period of time until it is completely dry. Finally, don't forget to wear protective gloves to avoid scalding your fingers.
Now you know why more and more people are trusting and relying on this small but powerful secret weapon! The next time you're faced with the need to solve some thorny problem and have no good plan, try it. There may be unexpected surprises waiting for you to find out.
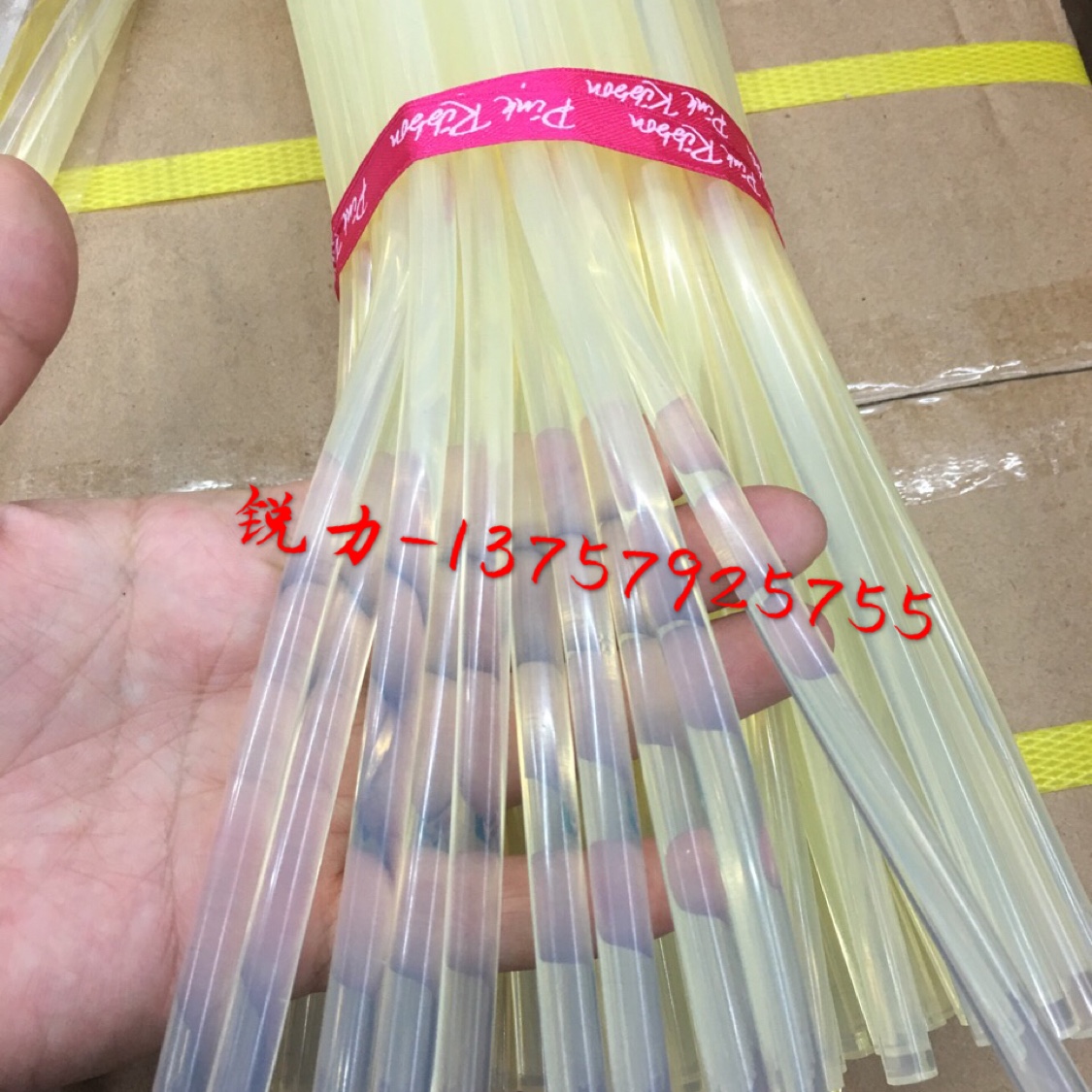